In the field of engineering, the pursuit of optimizing lightweight design while ensuring manufacturing feasibility has become a primary objective. Lightweight materials and structures offer a wide range of advantages, including improved efficiency, enhanced performance, and reduced environmental effects. However, achieving the balance between lightweight design and precision manufacturing poses significant challenges for prototyping services.
This article delves into the advanced strategies and considerations necessary for optimizing lightweight design without compromising manufacturing feasibility in industrial design prototyping.
Weight Reduction – Overall System
A comprehensive approach to lightweight design involves an in-depth analysis of the overall system to identify opportunities for weight reduction. By evaluating the weight, functionality, and structural requirements of product design prototype, you can pinpoint areas where reducing weight can yield significant results.
Finite element analysis (FEA) is used for precise structural analysis and optimization of lightweight components. Additionally, topology optimization methods can be employed to explore novel design solutions that maximize strength-to-weight ratios. This systems-level approach ensures that weight reduction efforts are strategically distributed across the system, optimizing performance, efficiency, and safety.
In addition to component-level weight reduction, streamlining the assembly process to reduce unnecessary weight and complexity can also be embedded in prototype manufacturing. Reducing the number of fixtures required during assembly, you can eliminate excess weight and simplify the manufacturing process. This can be replaced with innovative joining techniques, such as adhesive bonding or advanced fastening methods, leading to significant weight savings without compromising structural integrity.
Furthermore, for large assemblies, you must aim to minimize the number of redundant or duplicate parts in the overall system. Reducing unnecessary duplication not only reduces weight but also simplifies supply chain management and improves cost-effectiveness.
By carefully evaluating the functional requirements of each part and exploring opportunities for consolidation or redesign, you can eliminate redundancies and optimize the system’s weight-to-functionality ratio. Reducing the number of elements in an assembly is a general approach for weight reduction which leads to improved performance without compromising on the manufacturing efficiency.
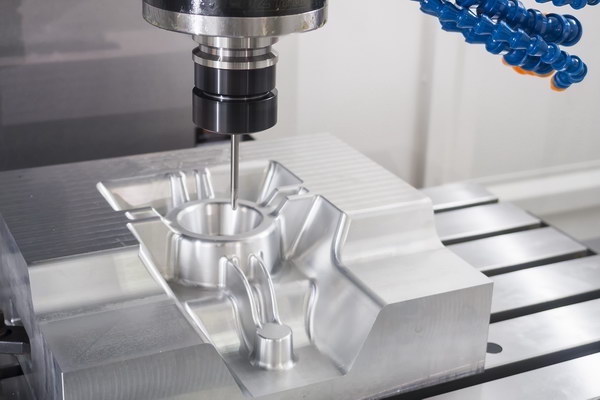
Alternative Materials Selection
The selection of appropriate materials is a critical aspect of lightweight design optimization. When considering lightweight design, a common comparison arises between steel and aluminum due to their widespread use in various industries. Both materials possess distinct advantages and disadvantages that must be carefully evaluated based on specific application requirements.
Although steel has been favored for its exceptional strength and durability in harsh manufacturing environments, recently aluminum has also deemed to be a suitable competitor for lightweight designs. However, the two materials must be used in prototypes as per their suitable properties. For example, steel outperforms in high-tensile environments and thus, it is an obvious choice. While, for pure bending conditions, aluminum is a better choice as compared to steel as it can not only perform better but also reduces the overall weight of the system by 40%.
Lately, fiber-reinforced materials, such as carbon fiber composites and fiberglass composites, have emerged as game-changers in industrial design prototyping for their remarkable lightweight properties and performance characteristics. They are widely used in rapid prototyping services due to their impact resistance and effective energy dissipation. You can use these materials to manufacture small and intricate designs as well as large aerodynamic designs as they are widely suitable for rapid prototyping. Additionally, fiber-reinforced composites boast high yield strength, enabling them to withstand substantial loads before going into plastic deformation.
Dealing with Residual Stresses
In advanced lightweight designs, addressing and managing residual stresses can be crucial for experts. Residual stresses can significantly impact the structural integrity, performance, and reliability of the final product. In order to tackle this challenge, the design must be analysed thoroughly using finite element analysis (FEA) and computational fluid dynamics (CFD) to predict and analyse residual stresses. These stresses must also be identified before prototype manufacturing. By simulating the entire production process, you can identify areas of high residual stresses and adjust design or manufacturing parameters to optimize the process.
Once the residual stresses are identified using FEA and CFD, various techniques can be employed to mitigate them at industrial design prototyping level. One such technique is the stress relief annealing which involves controlled heating and cooling cycles to relax internal stresses. In addition, heat treatment processes like solution treatment or aging can also be used to modify the material’s microstructure to relieve residual stresses. Mechanical surface treatments such as shot peening induce compressive stresses that help with counteracting the tensile residual stresses, thus, enhancing fatigue life and resistance to crack.
Reducing the weight of a component may lead to additional stresses that effects the structural integrity of the system. Therefore, thorough inspections and non-destructive testing are essential to validate stress mitigation and ensure integrity of lightweight components. Techniques like strain gauging, X-ray diffraction, and digital image correlation are useful to measure and analyse residual stresses after weight-reduction of a material. This feedback assists in further optimizing design and prototype manufacturing.
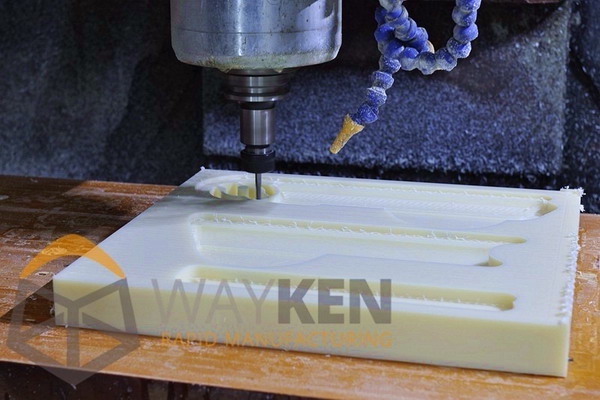
By utilizing advanced simulation tools, applying stress relief techniques, and conducting comprehensive inspections, you can effectively address and manage residual stresses. This ensures the long-term structural integrity, performance, and reliability of advanced lightweight designs. Managing residual stresses becomes difficult in optimizing lightweight designs for various industries. Therefore, a careful consideration and analysis is necessary to rule out any design failures.
Conclusion
In conclusion, it can be quite challenging to achieve optimised design with reduced weight while maintaining structural integrity and manufacturing feasibility. However, a systematic approach with a combination of design, analysis, testing and characterization helps in achieving the target. It is essential to select the right material for your application in terms of weight and also analyse the redundant and duplicate fixtures that are only adding weight to the design. Lastly, by analysing and managing residual stresses using advanced simulation and inspection methods, you can strike a balance between lightweight design and manufacturing feasibility.
Collaboration between engineering, design, and manufacturing teams, equipped with specialized knowledge and expertise, is crucial to successful lightweight design implementation. By embracing these advanced strategies and considerations, you can enjoy complete benefits of a lightweight design in addition to the remarkable improvements in performance, efficiency, and overall engineering excellence.